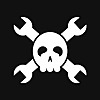
Hackaday | CNC Hacks
954 FOLLOWERS
Hackaday.com serves up fresh hacks each day, every day from around the web. Hackaday.io is a platform for people who like to make things. From electronics hacks to CNC hacks you can find all the hacks at one place here.
Hackaday | CNC Hacks
2d ago
The Mostly Printed CNC is famous for two things. First, being made mostly from 3D printed parts and commonly available steel tubing. Second, because of the materials used, its rigidity isn’t fantastic. But any CNC router is better than no CNC router, and [Alex Reiner]’s “Mostly Mostly Printed CNC” upgrades the base MPCNC into a much more capable unit.
MPCNC purists may want to look away, as the video below shows [Alex] committing the heresy of adding linear rails to his machine. The rails were sourced from VEVOR and at less than $100 for 10 meters, it must have been hard to resist. The rigidi ..read more
Hackaday | CNC Hacks
1w ago
[Daniel] has been metalworking on a budget for a while now. Originally doing things like plasma cutting on old bricks, he used his original plasma cutter to make an appropriate plasma cutting table complete with a water bath which we presume was not only safer but better for his back. Since then he’s stepped up a little more with what might be the lowest-cost CNC plasma cutter that can reliably be put together.
The CNC machine uses a handheld plasma cutting torch as its base, which uses a blowback start mechanism making it usable in an automated CNC setup without interfering with the control ..read more
Hackaday | CNC Hacks
3w ago
Workholding is generally not a problem on a big CNC plasma cutter.; gravity does a pretty good job of keeping heavy sheet steel in place on the bed. But what if your CNC table isn’t a table? The answer: magnets — lots of magnets.
The backstory on this is a bit involved, but the condensed version is that [Lucas] needed a CNC plasma cutter big enough to cut full-sized sheets of steel, but lacked the floor space in his shop for such a beast. His solution was to build a custom CNC machine that stands more or less vertically, allowing him to cut full sheets in a mere fraction of the floor space. I ..read more
Hackaday | CNC Hacks
1M ago
[enhydra] needed to modify a bunch of side inserts from some cheap ABS enclosures, and to save time and effort, he created a simple vacuum table with swappable inserts to precisely fit the parts. Suction is provided by a shop vacuum (plugged in near the bottom in the photo above) and it worked very well! Sealing and gaskets weren’t even required.
A vacuum table provides a way to hold workpieces flat and secure while a CNC machine does its thing, and because no clamps are involved, it can really speed up repetitive work. [enhydra]’s solution combines a vacuum table with a jig that ensures ever ..read more
Hackaday | CNC Hacks
1M ago
Thanks to 3D printing, most of us are familiar with the concept of additive manufacturing, and by extension, subtractive manufacturing. But what is it when you’re neither adding material nor taking it away to create something? Generally speaking, that’s called forming, and while there are tons of ways to do it, one you might not have heard of is single-point incremental forming (SPIF), and it’s pretty cool.
To explore SPIF as a method for making small parts, [Russell Makes] gave it a go on a small CNC mill. The idea is pretty simple, and the video below makes it pretty clear what’s going on ..read more
Hackaday | CNC Hacks
3M ago
The trouble with building a business around selling low-margin widgets is that you have to find a way to make a lot of them to make it worth your while. And if the widget in question is labor-intensive to make, you’ve got to find ways to reduce your inputs. That sounds like a job for industrial automation, a solution that’s often out of reach of small shops, for all the obvious reasons. Not if you’re clever about things, though, as this fully automated CNC lathe work cell shows.
This build comes to us from the woodshop of [Maher Lagha], where he’s making wooden honey dippers. Wooden dowel bla ..read more
Hackaday | CNC Hacks
4M ago
When you own an enormous CNC router, you’ve got to find projects that justify it. So why not shoot for the sky — literally — and build the 1980s-est possible thing: a full-scale flying Delorean.
Attentive readers will no doubt remember [Brian Brocken] from his recent attempt to bring a welding robot out of retirement. That worked quite well, and equipped with a high-speed spindle, the giant ABB robot is now one of the biggest CNC routers we’ve ever seen. As for the flying Delorean, short of the well-known Mr. Fusion mod, [Brian] had to settle for less fictional approaches. The project is stil ..read more
Hackaday | CNC Hacks
5M ago
Result of winding a carbon fiber tube. (Credit: Andrew Reilley)
Carbon fiber (CF) is an amazing material that provides a lot of strength for very little weight, making it very useful for a lot of applications, ranging from rods in CoreXY 3D printers to model- and full-sized rockets. The model rocketry hobby is the reason why [Andrew Reilley] developed his own CF tube winding machine called Contraption. A tutorial video (also embedded below) shows how this machine is prepped for a winding run, followed by the winding progress and finalizing before admiring the result.
The entire machine’s desi ..read more
Hackaday | CNC Hacks
6M ago
[Sebastian] describes himself as “a total noob” when it comes to CNC, so in an attempt to get to know his new CNC router, he chose about the most complex possible project — replicating an original Game Boy case in wood. And spoiler alert: he nailed it.
Of course, he did have a few things going for him. At least from a straight woodworking perspective, it’s hard to go wrong by choosing walnut as your material. Then again, it can be unforgiving at times, and picky about tooling, which is probably why [Sebastian] used nine different tools to get the job done. But where he upped the difficulty le ..read more
Hackaday | CNC Hacks
7M ago
There was a time when plotters were the pinnacle of computer graphics output. While they aren’t as common as they used to be, there are some advantages to having a plotter. [Symon] wanted a plotter and decided to make one from scratch. Truthfully, he wants to build a CNC machine, so the plotter is just a stepping stone. In fact, some of it may be a little much for just a plotter. Other design choices have worked for the plotter, but don’t look like they will work well for the eventual CNC design.
As an example, the plotter uses 2020 extrusions and lead screws. An Arduino with a CNC shield pro ..read more