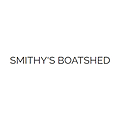
Smithy's Boatshed Blog
49 FOLLOWERS
I've had a long career building, repairing and restoring wooden boats, and although I've retired from commercial work I can't stop building boats. This site shows a lot of the boats I have worked on, as well as the current one I'm building. There's stuff also about my years of teaching boatbuilding, about boat festivals and about the history of the eighteen-footers and open..
Smithy's Boatshed Blog
3w ago
Lots of bits and pieces are turning up, like this Hydralign 14" 3-blade feathering propellor. It's now fitted and the shaft is connected to the engine which is now bolted down. I will have to disconnect it when I drill for the bolts through the deadwood later this year, but it will be a small job to move the engine and then return it for good.
The lead keel has been cast and delivered from Central Foundry in Mascot. They do superb castings, and it's the third keel casting I have had done by them since 2000. I did a couple of keels myself in the 1990's but decided it was much safer to get the ..read more
Smithy's Boatshed Blog
3w ago
Whoa! Looks like I neglected to post the link to Episode 23 and it's a couple of months old! Sorry about that if you missed it so far. It shows how I built the sliding companion hatch, the skylight and the forward hatch ..read more
Smithy's Boatshed Blog
7M ago
The companionway hatch, the skylight and the forehatch are all built and are currently part of the way through their varnishwork. I have chosen New Guinea Rosewood (Pterocarpus Indicus) as the timber to use. The original boats of the Ranger class mostly had hatches of Queensland Maple, and I seriously considered that, but several of them have replaced the Queensland Maple with Teak over the decades. I decided against Teak for two reasons: one was the cost, at least 3 times as much as the Rosewood; and the other was that it seems that much of the money made from Teak finds its way to the ..read more
Smithy's Boatshed Blog
1y ago
It took 3 days with other commitments, but I managed to sheathe the deck. I laid it in 8 separate panels, carefully planned to minimise the length of the joins, with the dynel cloth being exactly one metre wide. When I laid more than one contiguous panel on the one day I simply located the two pieces of cloth closely together with the narrowest of overlaps. When I started again the next day I sanded a feather edge on the old panel and placed two layers of masking tape around 1/2" (12mm) from the edge so the new panel would overlap slightly.
But as usual, preparation is the key to a suc ..read more
Smithy's Boatshed Blog
1y ago
As I described in the previous post, the deck is a combination of a layer of (9mm tongue-and-groove Western Red Cedar with a layer of 9mm (more like 10mm actually) Hoop Pine Marine Plywood over it. That layer now is all fitted, seven pieces in all, scarfed together with 75mm (3 inch) scarfs at every panel joint. Each panel was glued down with WEST System epoxy resin thickened with Microfibers and fastened through to the deck beams with a few 1 1/2" (38mm) silicon bronze woodscrews and many 1 1/4" (32mm) monel ring nails.
The first shot above shows the Port forward panel glued and fastened ..read more
Smithy's Boatshed Blog
1y ago
The portlights in the raised deck area of the hull have been fitted and so have the 6 chainplates. These were all easier to fit before I start laying the deck. Before I could fit the portholes it was best to undercoat the outside of the hull....and before I undercoated the hull I had to fit the chainplates so the bolt heads could be plugged, sanded and primed. And also the final coats of satin varnish were applied to the interior. You're looking at Huon Pine planking, Spotted Gum ribs and lower sheer clamp (with magnificent fiddleback grain), Celery Top Pine upper sheer clamp, Queensland Mapl ..read more
Smithy's Boatshed Blog
1y ago
The hull has been planked for a while, but in the Spring I started caulking, and after 115 hours spread over a few months the hull is completely caulked and the seams payed. The video shows all the tools, materials and methods, and I point out how we follow the English system in Australia, doing it a bit differently from the USA and Canada. Link https://youtu.be/0H1wDDVxJ-c ..read more
Smithy's Boatshed Blog
2y ago
I've begun to polish the bronze castings I received from Central Foundry and I've combined some footage of this with footage from earlier in the year when I made the patterns for the castings. Any traditional boat like this one needs bronze fittings. Many parts are available off the shelf, as we've seen with the portholes (Episode 15) and the seacocks (Episode 16), but many need to be custom made. if you do the pattern making and polishing yourself this can be relatively cheap. Here's how I did it. https://youtu.be/zv4movx_roU ..read more
Smithy's Boatshed Blog
2y ago
Normally you don't want water to enter your hull, but there are some exceptions: you may need cooling water for your engine, or for a salt water pump for the galley. You may also need to get rid of water or waste, like from the sink or from bilge pumps. You'll need seacocks so you can control the water movement. In this episode I show the several different types of seacocks, and discuss where they are located and how to fit them to a carvel=planked hull. Here's the link, seeing YouTube doesn't seem to work on this site anymore: https://youtu.be/pLEZoPbvLDI  ..read more
Smithy's Boatshed Blog
2y ago
The latest episode shows how I fitted the opening portholes to the raised deck area of the topsides. I cover the methods used as well as some advice on locating portholes on topsides and on cabin sides for the best appearance. It's on youtu.be/x6ekXaO0lF8 ..read more