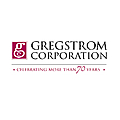
Gregstrom Corporation Blog
4 FOLLOWERS
Gregstrom's plastics blog is the place to learn more about custom rotational molding, heavy-gauge thermoforming, and a full range of assembly and testing services that adds value to your plastics projects. Gregstrom Corporation is a Made in the USA rotational molding company that provides value-added services like assembly and testing.
Gregstrom Corporation Blog
6d ago
Molded-in holes can reduce part costs by eliminating the need for secondary machining. The benefits don’t end there. Generally, holes that are molded into a plastic part are stronger than holes that are machined. Machined holes are also subject to variations during drilling or routing. By contrast, molded-in holes have a size and position that are fixed because they’re part of the mold.
Rotational Molding vs. Injection Molding
Rotational molding supports the use of holes that are molded through, into, and onto plastic parts. Injection molding can also produce molded-in holes, but at the risk o ..read more
Gregstrom Corporation Blog
1M ago
Rotational molding can produce hollow parts with closely-spaced parallel walls. Examples include insulated coolers, plastic boats and bins, and cushioned shipping cases. When designing parts like this, however, it’s important to understand how rotomolding works so that you leave enough room between the walls.
Powdered Plastic and Parallel Walls
The powdered plastic that’s used in rotomolding has a bulk density that’s greater than when this same material is molded into a finished part. Many factors that affect bulk density, including the amount of air that’s trapped in the particles (occluded a ..read more
Gregstrom Corporation Blog
2M ago
Undercuts are used to create slots, screw threads, side holes, locking tabs, barbed fittings, and other part features. Rotational molding isn’t the only plastics process that supports the design and manufacturing of undercuts, but it’s easier to produce them with rotomolded parts than with injection molded ones.
If you’re comparing processes for your next plastics project, remember to include undercuts in your design for manufacturability (DFM) considerations. Undercuts can create valuable design elements that secure connections, replace metal fasteners, and provide access to buttons inside en ..read more
Gregstrom Corporation Blog
3M ago
Corner radii are angles at the internal and external corners of a part. They add strength by distributing stresses. For designers, this Q&A from Gregstrom provides answers to some frequently asked questions about corner radii in rotomolded products.
What is a corner radius used for?
In rotational molding, a corner radius serves two purposes. First, it distributes stress from the corner of a part over a broader area. Second, it improves quality by ensuring the adequate build-up of plastic material in the corner of a rotomolded part.
Why are sharp inside corners a problem?
In a metal mold, s ..read more
Gregstrom Corporation Blog
4M ago
North Pole – December 18, 2023 – Santa’s Workshop has confirmed reports that a pre-Christmas mishap involving Santa’s sleigh won’t stop the on-time delivery of presents this year. The flying-reindeer-powered vehicle was undamaged after hitting a bump during an unauthorized takeoff last weekend. The elves who attempted what the North Pole is calling a “joy ride” were not injured when Santa’s Sleigh overturned.
“I’m just glad that no one was hurt,” Santa Claus said in a rare pre-holiday interview that did not involve his appearance at a shopping mall. “When Mrs. Claus and I ordered a rotomolded ..read more
Gregstrom Corporation Blog
5M ago
Rotomolded ribs reinforce parts and help keep nominal wall thickness to a minimum. That’s important because thicker walls add material costs and increase cycle times. This Q&A from Gregstrom provides answers to some commonly asked questions about reinforcing ribs. For rotational molding that’s backed by experienced design assistance, contact us for a quote.
How are rotomolded ribs different from injection-molded ribs?
Unlike plastic injection molding, rotational molding uses hollow ribs instead of solid ones. There is an important exception, however. Rotomolding supports the use of molded ..read more
Gregstrom Corporation Blog
6M ago
Rotational molding is a plastics manufacturing process that can produce hollow parts in various sizes, colors, and textures. It also supports features, such as tapers and undercuts, which can be difficult to injection mold. Rotomolding offers part designers many advantages, but its low tooling costs, part quality, and part strength are especially attractive. Keep reading to learn more, and contact Gregstrom for a rotational molding quote.
Low Tooling Costs
Compared to plastic injection molding, rotational molding is a relatively low-pressure process. Consequently, rotational molds can use less ..read more
Gregstrom Corporation Blog
7M ago
Molds for rotational molding are inexpensive and lightweight. They can be as simple as a round object or support features such as ribs, undercuts, and tapers. Two-piece molds are typical, but three-piece molds are sometimes required for part removal. Regardless of the number of pieces, the tooling that’s used in rotational molding does not require coring or cooling.
Part Design and Mold Design
For part designers, mold selection depends on the size, shape, and surface finish of the part to be molded. For higher-volume projects, it’s also worth considering the number of molds that are needed. Th ..read more
Gregstrom Corporation Blog
8M ago
Polyethylene rotational molding can use either linear low-density polyethylene (LLDPE) or high-density polyethylene (HDPE) to produce strong, hollow parts for indoor and outdoor applications. LLDPE and HDPE are similar in terms of chemical composition but have some important differences when it comes to performance properties. This Q&A from Gregstrom examines these two rotomolding materials.
How are LLDPE and HDPE rotationally molded?
LLDPE and HDPE use the same basic process during rotational molding. First, powdered plastic or plastic pellets are added to a metal mold. Next, the tool is ..read more
Gregstrom Corporation Blog
9M ago
Polypropylene rotational molding uses polypropylene (PP) plastic to produce strong, hollow parts for both outdoor and indoor applications. This Q&A from Gregstrom provides an overview of rotomolding with polypropylene, one of the many materials we work with at our Made in USA manufacturing facility in Woburn, Massachusetts.
What are the advantages of polypropylene?
Polypropylene has excellent fatigue resistance and can withstand repeated loads. This thermoplastic also resists stress even when flexed and won’t react with a wide range of acids and bases. In addition to chemical resistance, P ..read more