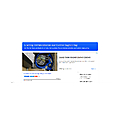
Learning Instrumentation And Control Engineering
38 FOLLOWERS
We Provide Tools and Basic Information for Learning Process Instrumentation and Control Engineering.
Learning Instrumentation And Control Engineering
1y ago
Design of Instrument Air System
Every plant requires instrument air system for some form of pneumatic control. The design of the design, sizing and distribution of instrument air is different from plant to plant depending on the location, the environment, and the number of instruments to be supplied instrument gas.
Below is illustrated a typical instrument air system design that you will find in a typical plant. Note that the blocks 1 to 5 illustrated in the schematic below are typically part of a vendor package. The vendor supplies these units as a package:
Sizing and Distribution
Norm ..read more
Learning Instrumentation And Control Engineering
1y ago
Orifice plates are the most common flow device you will find in any process plant. Although not very high in accuracy but they are rugged, have low maintenance cost and have been applied successfully in process instrumentation to measure flow.
Listed in the table below are recommended practices when it comes to industrial application of Orifice plates:
Recommended Practice in the Use of Orifice Plates
1
Orifice plates, with flange taps, square edge and concentric orifice are normally used on pipe sizes from 2” and above.
2
Eccentric or Segmental orifice plates ar ..read more
Learning Instrumentation And Control Engineering
1y ago
In process control design process variables such as temperature, pressure, flow, level, valve signals, analyzers etc are ranged in such a manner to be proportional to the primary signal as much as possible for control purposes. The table below shows the typical instrument scales employed in process control system design:
Instrument Variable
Scale
Temperature
Direct Reading
Pressure
Direct Reading
Flow (differential)
0 – 100 linear
Flow (Linearized)
0 – 100 linear
Level
0 – 100 linear
Analyzer
Direct Reading
Signal to Valves
0 – 100%
As far as ..read more
Learning Instrumentation And Control Engineering
1y ago
All installed process instruments in hazardous areas are required to have a type of protection that ensures safety of personnel as well as that of the instruments.
The following table provides the guidelines to select the type of protection according to the zone of risk:
Type of Protection
Meaning
Ex i
Intrinsic Safety
Ex d
Flameproof Enclosure
Ex e
Increased Safety
Ex m
Encapsulation
Ex p
Pressurized Apparatus
Device
Zone 0
Zone 1
Zone 2
Transmitter/Positioner
Ex i
Ex i (preferred)
Ex d (alternative)
Ex i (preferred)
Ex d, Ex ..read more
Learning Instrumentation And Control Engineering
1y ago
Control valves can be built from various combinations of valve actuator and valve body. The combination of actuator and valve body is usually chosen to provide a particular failure mode should the instrument air supply fail for any reason.
The most common control valve actuator used in the industry is the diaphragm actuator. Diaphragm actuators, as in the case of valve bodies, can be classified as either direct or reverse acting.
Read Also : Control Valve Actuators: Basic Types and Designs
Any failure mode can be obtained with a combination of direct or reverse acting
actuator and di ..read more
Learning Instrumentation And Control Engineering
1y ago
In many process control applications in industry, it is sometimes desirable to have multiple control valves respond to the output of a single common controller. Control valves configured in this way to follow the command of a single controller are said to be split-ranged, or sequenced.
Split-ranged control valves may assume different forms of sequencing. Common modes of control valve sequencing seen in the process industry are: complementary, exclusive, and progressive.
Complementary Split-Range Control
With this form of split-ranging, there is never a condition in the controller’s ou ..read more
Learning Instrumentation And Control Engineering
1y ago
A self operated pressure reducing regulator is a mechanical device that is used to control and reduce pressure especially in natural gas plants. A pressure regulator is essentially a force balanced device that adjusts to changes in the system it is controlling. There are two types of pressure reducing regulators used in natural gas systems:
1. Self operated regulators
2. Pilot operated regulators
Both types of regulators are very common in the gas industry the self-operated regulators are general used in lower flow and lower pressure system, and are less expensive regulators. While the pilot ..read more
Learning Instrumentation And Control Engineering
1y ago
A process transmitter typically ”measures” a process variable – flow, level, temperature, pressure - and produces an output in response to changes in the input variable. Most transmitters incorporates a sensor which measures the input variable and gives out an output of which 4 – 20m A is common.
Of critical importance in the performance of a transmitter is a concept called damping. As the input variable changes, the transmitter output must update and change accordingly. Damping is the amount of time required, in addition to the update time, for the output of the transmitter to reach 63.2 ..read more
Learning Instrumentation And Control Engineering
1y ago
The Maximum allowable non-shock pressure (psig) and temperature ratings for steel pipe flanges and flanged fittings according the American National Standard ANSI B16.5 are given in the table below.
Flanges and their Fittings are a common feature in the process plants. The need to accurately determine their pressure rating and corresponding temperature ratings is important for personnel and plant safety and overall plant performance and reliability:
Maximum Allowable Non-Shock Pressure (Psig)
Temperature (°F)
Pressure Class (lb)
150
300
400
600
900
1500
2500 ..read more
Learning Instrumentation And Control Engineering
1y ago
Control valves abound in every area of industrial process control. Control valves handle all kinds of fluids at temperatures from the cryogenic range to well over 1000°F (538°C). Selection of a control valve body assembly requires particular consideration to provide the best available combination of valve body style, material, and trim construction design for the intended service. Capacity requirements and system operating pressure ranges also must be considered in selecting a control valve to ensure satisfactory operation without undue initial expense.
Information required to sel ..read more