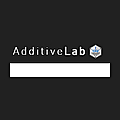
AdditiveLab Blog
27 FOLLOWERS
AdditiveLab Metal AM Simulation blogs talk about the application of simulation in Metal Additive Manufacturing. AdditiveLab has been specifically developed to address the engineering needs of Additive Manufacturing.
AdditiveLab Blog
2w ago
Distortion compensation based on 3D scan data is manifesting its crucial role in refining the precision of additively manufactured components. During the additive manufacturing process, distortions may occur due to factors such as thermal effects, residual stresses, or material variations. By leveraging 3D scanning technology, users can capture the actual geometrical deviations of the fabricated part from the intended design. Utilizing scan data enables the development of distortion compensation strategies, where adjustments to the original CAD model can be made to account for the observed dis ..read more
AdditiveLab Blog
2w ago
Process optimization in metal 3D printing focuses on maximizing the efficiency, speed, and quality of the additive manufacturing process. Finite Element (FE) simulation plays a crucial role in this optimization by providing insights into the complex thermal, mechanical, and metallurgical phenomena occurring during printing.
Here's how FE simulation can help with process optimization:
Predicting Thermal Behavior
Thermal load illustrated on structure with different attachment strategies to build plate.
FE simulation can calculate the heat transfer within the build chamber, the melting ..read more
AdditiveLab Blog
2w ago
Introduction
Metal Additive Manufacturing (AM) has revolutionized the manufacturing industry by enabling the production of complex geometries with high precision. However, achieving successful prints often relies on proper Support placement to mitigate deformations and ensure structural integrity.
Support structures are crucial in metal AM to prevent deformations, warping, and structural failures during the printing process. As metals undergo thermal expansion and contraction, Supports hold the overhanging or intricate features of the design in place, preventing them from collapsing ..read more
AdditiveLab Blog
11M ago
In metal Additive Manufacturing, a Process Map is a graphical representation of the relationship between power and speed settings during the manufacturing process. It involves plotting different combinations of power and speed on a diagram to understand their impact on the quality of the manufactured part and it is used to analyze and optimize laser-based additive manufacturing processes.
Sample Process Map
In a Process Map, the power level of the laser is plotted on the vertical axis, while the scanning speed of the laser beam is plotted on the horizontal axis. By varying these parameters, o ..read more
AdditiveLab Blog
1y ago
Metal Additive Manufacturing (AM) is an innovative technology that allows for the direct production of intricate metal parts via depositing metal powder layer by layer and selectively melting and fusing it to fabricate the final component.
By subjecting the deposited material surface to a heat source, such as a laser beam, an intense heating effect takes place, rapidly elevating the temperature of the material. As the temperature exceeds the metal's melting point, the material undergoes a phase transition, transforming into a liquid state of molten metal, forming a distinct pool referred to as ..read more
AdditiveLab Blog
1y ago
Look at the process parameters above. In your opinion, does the proposed parameter-set cause a (A) keyhole-mode or a (B) conductive-mode melt-pool formation and why?
Recently we published a post asking metal AM enthusiasts their opinion about a set of AM process parameters and whether they would cause (A) a keyhole-mode or (B) a conductive-mode melt-pool formation and why.
We performed a metal AM process simulation via the Scanning-path module in the AdditiveLab software and concluded the correct answer is A, it causes a keyhole-mode melt-pool formation.
The results are depicted in the image ..read more
AdditiveLab Blog
2y ago
Look at the image above; in your opinion, which Part-Support configuration will experience the LEAST deformation of the final Part.
More info in regard to the Part-Support configuration:
- Part: wheel bearing structure
- Support: Predominantly cone supports
- Material: Ti6Al4V
- AM process: LPBF
- Deformation of the final Part: The deformation that occurs once the configuration is removed from the building plate and the Supports are removed from the Part.
Recently we published a post asking metal AM enthusiasts their opinion about three Part-Support configurations (A, B or C) and which one wo ..read more
AdditiveLab Blog
2y ago
AdditiveLab’s melt pool simulation can be utilized to investigate the influence of different machine settings on melt pool geometry. This can ensure that material is melted properly while reducing the risk of material overheating and evaporation. AdditiveLab empowers to create customized melt pool simulations within moments to enable users to efficiently narrow down possible machine settings for successful metal prints ..read more
AdditiveLab Blog
2y ago
The workflow for Additive Manufacturing (AM) simulations can be quite simplified. In AdditiveLab for example, AM simulations of part-support configurations can be performed with only a couple of clicks. However, having generated simulation results often is not enough to determine whether a build configuration will fail.
Traditional Engineering Assessments vs. Additive Manufacturing Process Assessments
In traditional structural engineering, simulation-based assessments of potential failures are commonly done based on defined and standardized strength assessment strategies. For example, strengt ..read more
AdditiveLab Blog
2y ago
https://video.wixstatic.com/video/72d41c_677eb2803e174b008a25406c82804435/1080p/mp4/file.mp4 ..read more